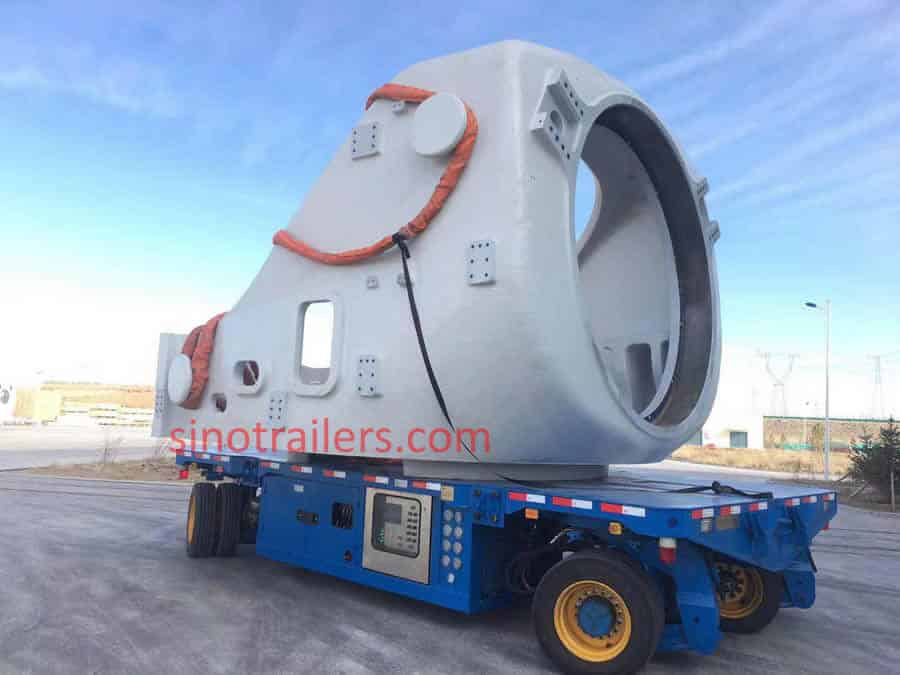
What is electric SPMT
As a type of new energy vehicle, the electric SPMT is different from the conventional, diesel engine motorized SPMT transporter, the purpose of the battery-driven electric SPMT transporter is to provide in-plant transportation solutions for oversized and super-heavy cargos.
In simple words, electric SPMT is using battery to supply power for the self-propelled modular transporter, not the high power diesel engine.
Advantages of electric SPMT
Compare to conventional SPMT, electric SPMT has no worry of emissions and noise. Make use of a high volume of lithium battery, it can be converted auto guided vehicle(AGV) easily.
From project logistics to industrial logistics
Conventioal SPMT(diesel enginer SPMT) is the main role in project logistics for many years. With the help of battery PPU, the electric SPMT can enter the industrial logistics easily.
Electric SPMT in China
Electric SPMT has a growing demand in China an other markets near China.
Comparison of electric SPMT with diesel engine SPMT
Volume limination of PPU
Due to the high emission standards and environmental protection requirements, the volume of the high power diesel engine is getting bigger to meet with the standards.
If the working conditions need the self-propelled modular transporter to be smaller, we can not use the traditional high-power diesel engine, we have to choose the battery-driven PPU to drive the SPMT.
One of the advantages of the electric SPMT is that the shape of the battery is changeable according to the SPMT size, in other words, we can customize the dimensions of the lithium battery, which can easily ensure its trafficability.
Balance axle pendulum hydraulic suspension
It is conventional suspension, most hydraulic trailers and self-propelled modular transporters are using this type of suspension. It is simply like an arm holding a dumbbell. The arm is the suspension arm, we can regard the dumbbell as the balance axle. After the suspension arm coupling with the cylinder, it can open and close like an arm lifting a dumbbell to realize the change of its height and then lift and lower the height of the SPMT.
Because the center point of the axle is not at the same point as the center point of the pendulum suspension, the chassis of the SPMT may have slight displacement against the suspension and tires during the steering process, which probably will affect the positioning accuracy of the transporter.
Single pilar concentric hydraulic suspension
The suspension of the electric SPMT can adopt the new single-pilar concentric hydraulic independent suspension system. This kind of suspension system has higher accuracy and can improve the guidance accuracy of the SPMT to the millimeter level.
The improvement of accuracy can firstly improve the accuracy of the assembly of cargo. For example, when welding two ship hulls, the single pilar concentric suspension can do a better job. Secondly, it can also match the navigation accuracy requirements in the transition from electric SPMT to electric heavy-duty AGVs, and improve the accuracy of unmanned driving and automatic navigation, and enhance the safety of driving.
Electric motor-driven steering system
The steering accuracy of the electric motor-driven steering system is higher than that of the hydraulic transmission steering system. The reason is the hydraulic system may have oil leakage(pressure drop) and efficiency problems, leading to its performance is not very stable in the application where requiring high accuracy positioning. The electric motor-driving steering system can just make up for this problem. At the same time, when the whole self-propelled modular transporter uses electric power, it can improve the power efficiency and further increase the operation time after a single charging.
Lower nosie and no emission
Due to no diesel engine involved, the noise of electric SPMT can be at a very low level.
Electric SPMT has no emission, available in dust-free plant.
Lower cost for procument and use
Most high power diesel engines are from EU, the total cost is high if we consider the freight and import duty.
If we use the lithium battery, we can buy it directly from China, the cost was high as well. But thanks to the rapid development of the lithium battery industry, the cost is getting lower.
Now, the lithium battery is cheap enough to replace the European diesel engine, especially in China and other countries in Asia. In the future, the battery will be an advantage for new energy vehicles after we can quick-charge batteries.
As for the cost to use, we can lower the cost up to 60% if we use the battery instead of the diesel engine.
Electric SPMT vs. AGV
The electric SPMT is easier to upgrade into AGV. But SPMT AGV is different from the ordinary AGV that already existing in the market.
Advantages of SPMT type AGV
With higher carrying capacity. The capacity of ordinary AGV is generally from hundreds of kilograms to dozens of tons. The AGV upgraded from the electric self-propelled modular transporter has much more carrying capacity. Even the smallest SPMT 2-axle module can carry more than 60 tons cargo.
With lifting and lowing function. The function makes the transporter has compensation for uneven road conditions, which can increase the trafficability and safety of goods transition. And it can use rubber tire, polyurethane filled tire and polyurethane tire.
Basic Designs of Battery SPMT
The structure design of the battery SPMT is reasonable, with sufficient static, dynamic stiffness, high stability, and high reliability, and adopting the newest technology to ensure that the system and mechanism have good dynamic quality.
The transporter has its own power and adopts hydrostatic driving. It can realize multi-mode independent steering and platform lifting functions. It can be controlled remotely. It can arbitrarily combine and combine the transportation transporter as groups according to the characteristics of the transported goods (external dimensions, tonnage). Thus, it can realize the transportation of extra-large tonnage objects.
During transportation, the operation of the electric transporter is safe, stable and easy to operate.
Sourcing Parts
The selected components of the electric self-propelled modular transporter have high accuracy, good reliability, fast response speed, convenient operation and maintenance, malfunction display, good appearance, excellent after-sales service and high quality.
Design Standards
European Machinery Directive: 2006/42/EC
European Union Standards: EN1915-1, EN1915-2, EN12312-11, EN60204-1, IEC1346-1
Technical Configuration of Electric SPMT
The electric SPMT transporter transportation system mainly includes two major components: the electric SPMT and the power unit (hereinafter referred to as PPU). In order to fulfill the transportation of heavy goods of various weights and sizes, this multifunctional transportation system has the following technical features.
The electric self-propelled modular transporter is a multi-axle transporter equipped with a hydrostatic drive unit, an electronically controlled multi-directional steering unit, and a hydraulic lift loading unit. It is part of a modular combination transport system suitable for transporting various heavy loads. It can be moved underneath the cargo to load it, or the cargo can be loaded by other cranes. The loading platform is fully covered and freely accessible. The electric SPMT is equipped with the necessary hydraulic hoses and quick coupling connectors to connect with other electric SPMTs. Hydraulic pipes and coupling fittings are protected against corrosion, and the fittings are equipped with protective caps.
Chassis
The chassis frame of electric SPMT is welding with high-quality, low-alloy and high-strength structural steel Q690E. The mainframe is a box-shaped cross-section, and suspensions will be installed under transversely cross-beam.
The lower part of the two ends of the chassis frame has hinge connecting pins, and the upper part is with connection holes for connecting bolts in the latitudinal combination with other electric transporters.
The main chassis frame is equally connecting with bolt holes on both sides in the longitudinal direction, which are using the latitudinal combination of SPMTs (through the connecting blocks) or for the connection of turntable bolsters.
Suspension
The suspension of the electric SPMT is consisting of a suspension bracket, a balancing arm, a lifting cylinder, and an axle. The axles are further dividing into a drive axle and a brake axle. A hydraulic cylinder is to support the suspension bracket and the balancing arm. Tires adopt polyurethane-filled tires.
Hydraulic Lifting System
The hydraulic cylinders in the suspension are interconnecting with hydraulic steel pipes and hoses. Use a stop valve (ball valve) to divide the lifting cylinders. Depending on the weight of the cargo, the position of the center of gravity, and the road conditions, the lifting system can be divided into 3 or up to 4 points support, which are also applicable when multiple electric SPMTs are in combination. In this way, even on irregular roads, a uniform axle load can be ensured.
Each axle has a ball valve between the hydraulic circuits so that in the case of multiple transporters connection, the hydraulic system can also be flexibly dividing into groups. In the case of tire replacement or single axle malfunction, the suspension can be in lock mode or separating from the overall hydraulic system by manually operating the ball valve.
Safety System
The hydraulic lifting system has a single hydraulic circuit safety system to ensure that the electric SPMT will not tilt if any leakage appears in the hydraulic lifting circuit.
PPU
The PPU provides the hydraulic power source and electricity for the electric SPMT, the location of the PPT is under the chassis frame. The PPU can control the hydraulic groups in the electric SPMT individually or simultaneously to perform precise lifting operations of the cargo.
Drive System
The hydrostatic drive system is a “closed-loop” system. The drive axle has planetary drive gear and a variable pump to provide pressured hydraulic oil. We can adjust the displacement of the pump according to the speed of the diesel engine and the pressure ratio of the hydraulic motor, so as to continuously control the driving speed. The driving speed should automatically adapt to the running resistance and the gradient resistance, allowing the electric SPMT to start running and decelerate smoothly without shock and impact on the power system.
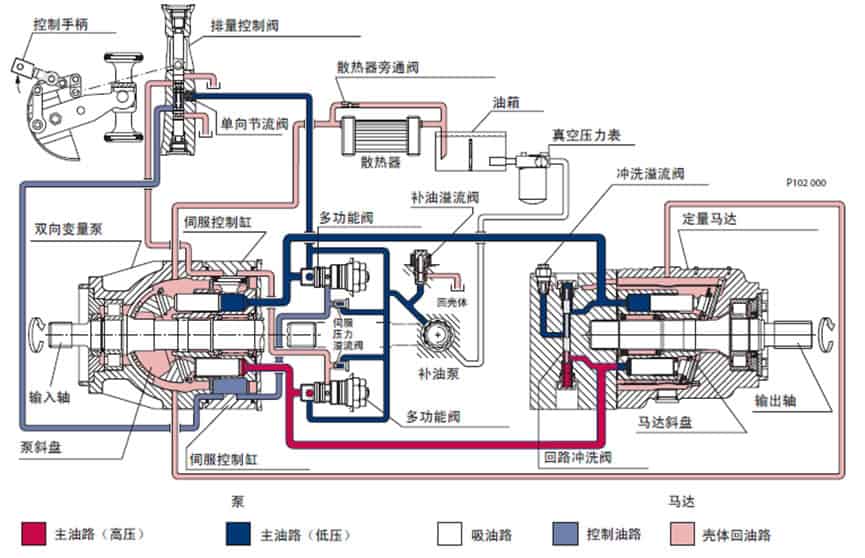
Motor speed is controlled electronically via a remote control system:
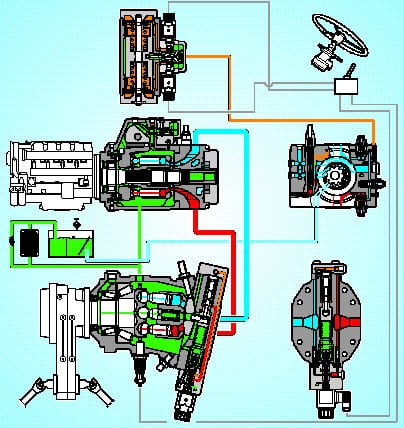
Electric-Hydraulic Multi-Modes Steering System
The suspension steering system includes electronic steering program and modular worm and gear steering (steering angle is from +130° to -130°)
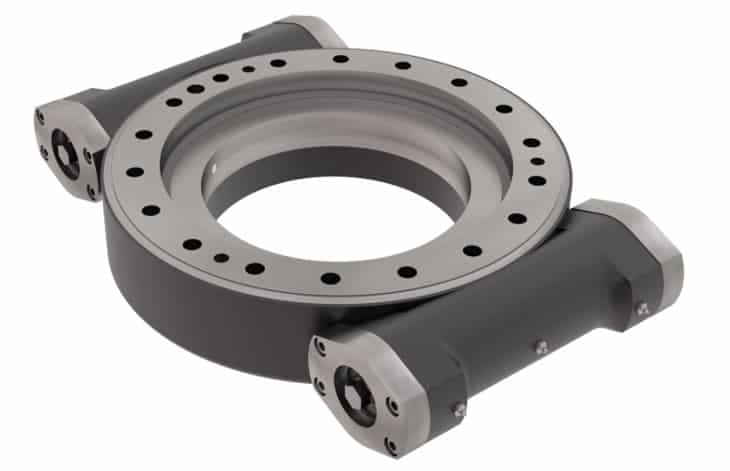
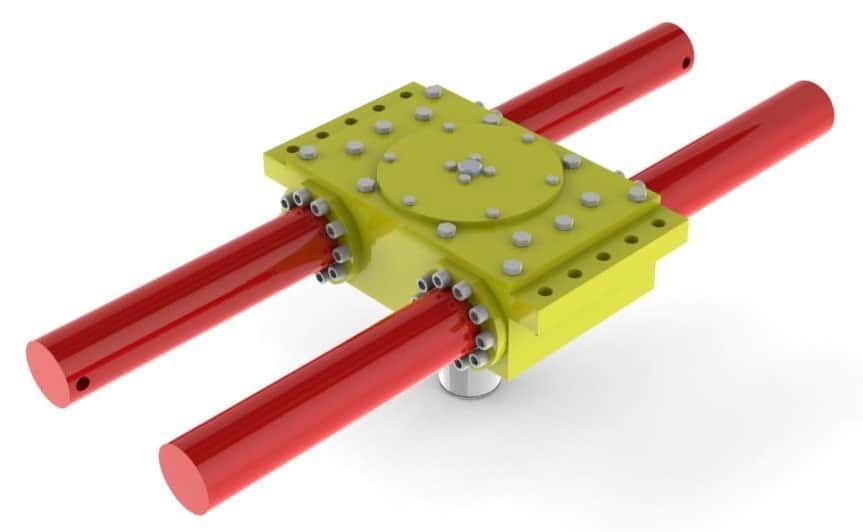
The worm gear steering mechanism adopts a modular design, which is connecting to the chassis frame by high tensile bolts and has good maintainability. At the same time, the load capacity is 25 tons, and the rated output torque can reach 50000N.m. It has been proved through practical use that the steering is flexible and reliable, and the steering pressure is low at full load. The closed lubrication structure is adopted, and the maintenance period is long.
Steering modes include longitudinal and lateral all-wheel steering, normal steering, and center rotating. For the soft connection configuration of the electric SPMT, the rotation center can be any point, that is allowing the transporter to move in any direction. Steering and changing the steering modes are possible when the electric SPMT is static and with a full load. In this way, precise lifting and transportation of the maximum load can be achieved.
ASR System
The drive axle has an electronic over-speed prevention system and a speed sensor on each drive axle. During the driving process, the microelectronic system monitors the actual slip rate of the drive wheels in real-time. The micro-electric system immediately generated a signal to reduce the motor displacement of the driving wheel, thereby ensuring the traction of the remaining driving wheels and achieving anti-slip control to prevent excessive rotation of the driving tire on smooth roads. The schematic of anti-slip control is shown in the figure below:
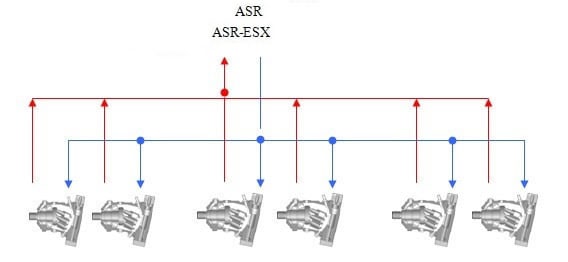
Electronic Diagnostics and Steering Tracking System
Electronic diagnostics and steering tracking systems are part of the electronic steering program. It can realize the correction of the angular position of the suspension and the diagnosis of the steering control circuit. On the control panel, the suspension can be turned into a maintenance mode.
Brake System
The brake system of the electric SPMT is hydraulic-mechanical maintenance and parking brake system. The brake is normally in close position, and the brake is releasing by the pressure of the hydraulic cylinder.
Electrical System
The auxiliary electrical system of the electric SPMT is a 24V-DC system. The electric SPMT has a lighting system at the front and back as necessary. Electric wires, distributors, and connectors to facilitate the transmission of power and control instructions, and it can connect with other electric SPMTs also. Electrical and electronic switches and control components are installed in shock-proof junction boxes. Circuits and components should be labeled in accordance with standards to facilitate malfunction lookup and repair. The junction box should be made of stainless steel and meet the IP67 protection standard.
Combination of Electric Transporters
The combination of the electric SPMT transporters network can form a 100m × 100m transportation platform. The distance between two electric SPMTs can reach 100m and can move and lift synchronously.
Coating and Painting
Before painting, the steel body of the electric SPMT is sandblasted, and the sand is in accordance with SIS 05 5900-SA 2 1/2 or DIN 55928-4, 2 grades. The two-layer primer with a dry film thickness of 50µm and topcoat with a dry film thickness of 50µm and the total dry film thickness is 150µm. The customer can choose SPMT’s color, and metal parts without painting are coating with chrome.
Working Environment
The electric SPMT working temperature range from -30°C to +50°C and relative humidity is 95%.
Steering Modes
Different from the linkage steering of multi-axle modular trailers, each suspension pendulum of electric SPMT is independent, and the steering angle is more 180 degrees.
All-wheel steering (any point rotation)
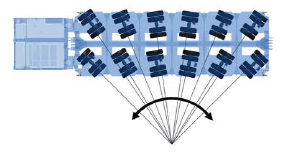
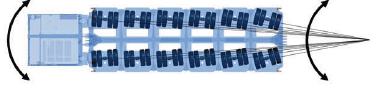
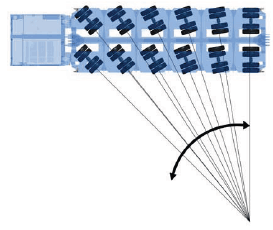
Diagonal Steering
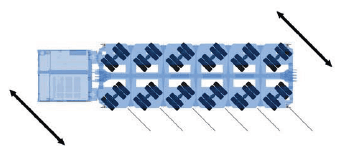
Lateral Move Steering
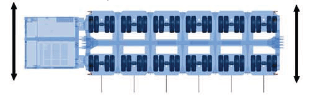
Center Rotate Steering
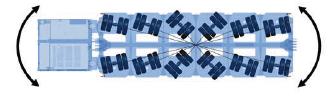
Performance Curve Diagram
Relationship between lifting force and axle load
20t chassis frame in static status, this figure can be used to determine the number of pendulum axle, when the hydraulic lifting force is divided into four groups of A, B, C, and D, and the force in the range of ± 5% of rated load. It also can be used to determine that if the four groups of pressure values showed the same reading, it indicates that the center of gravity of the payload is in the most ideal position.
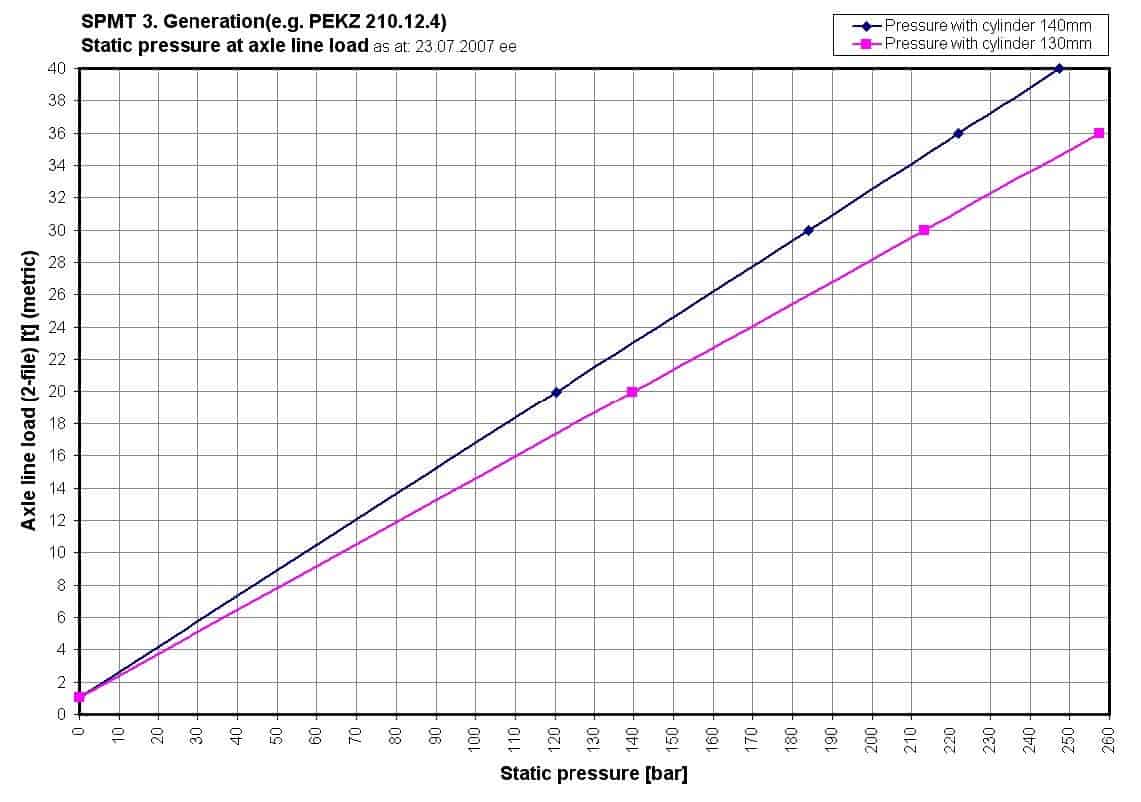
Before taking a pressure reading, please note:
- Park the electric SPMT on level ground.
- Park the electric SPMT at the driving height (middle height postion).
- The brake is in release mode.
- Wait for 10 to 20 seconds before taking a pressure reading.
Relationship Between the Quantity of Axle-line and Effective Load
This graph can be used to determine the number of axles required for a given payload. Conversely, it can be used to determine the payload for a given quantity of axle-lines.
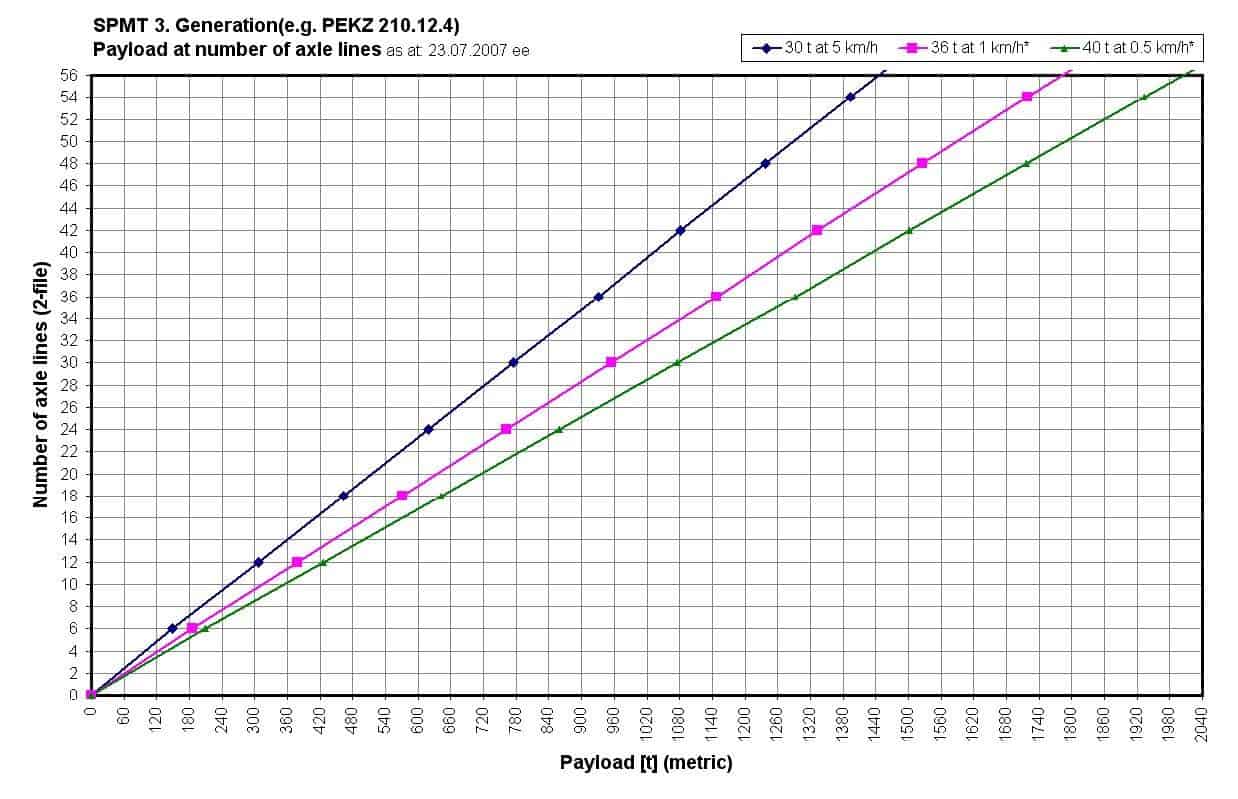
Relationship Between the Quantity of Drive Axle and Total Weight
This graph can be used to determine the number of drive axles required for a given total weight. Conversely, it can be used to determine the total weight for a given quantity of drive axles.
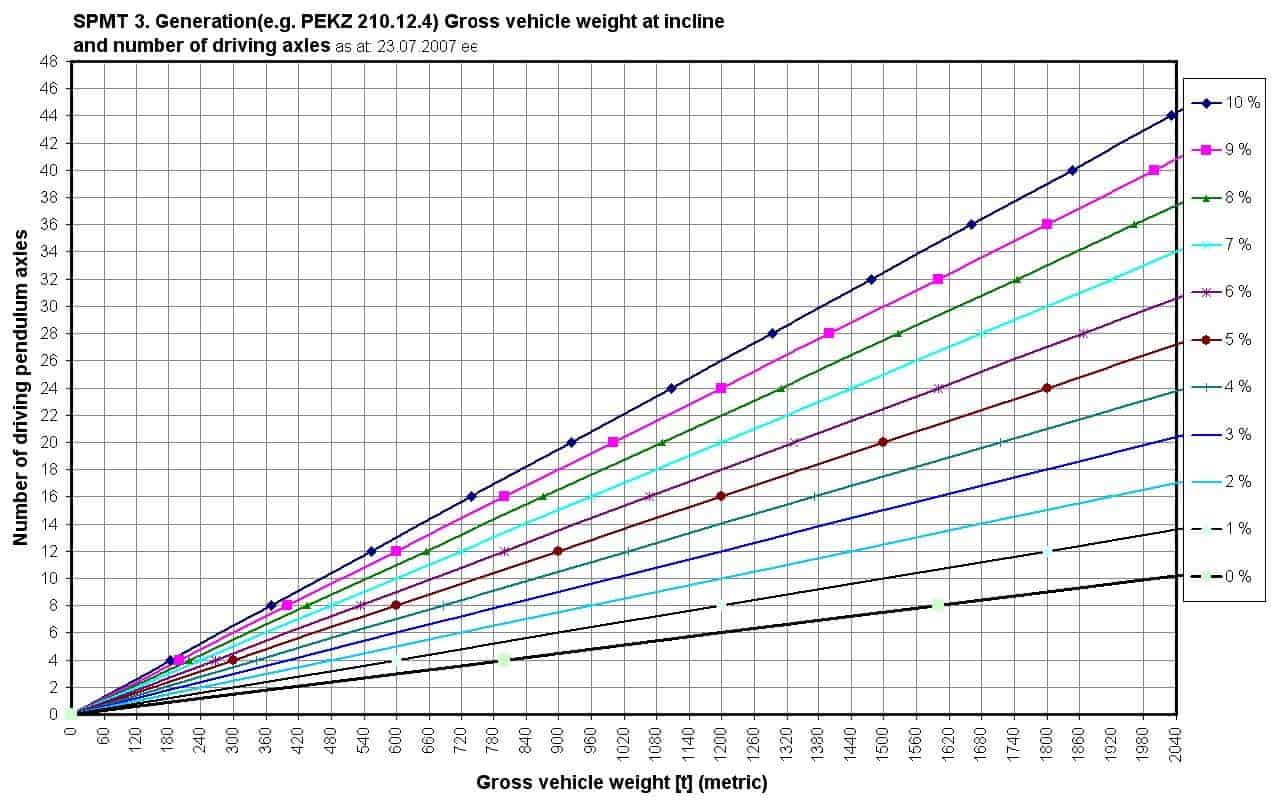
Remote Controller
Including:
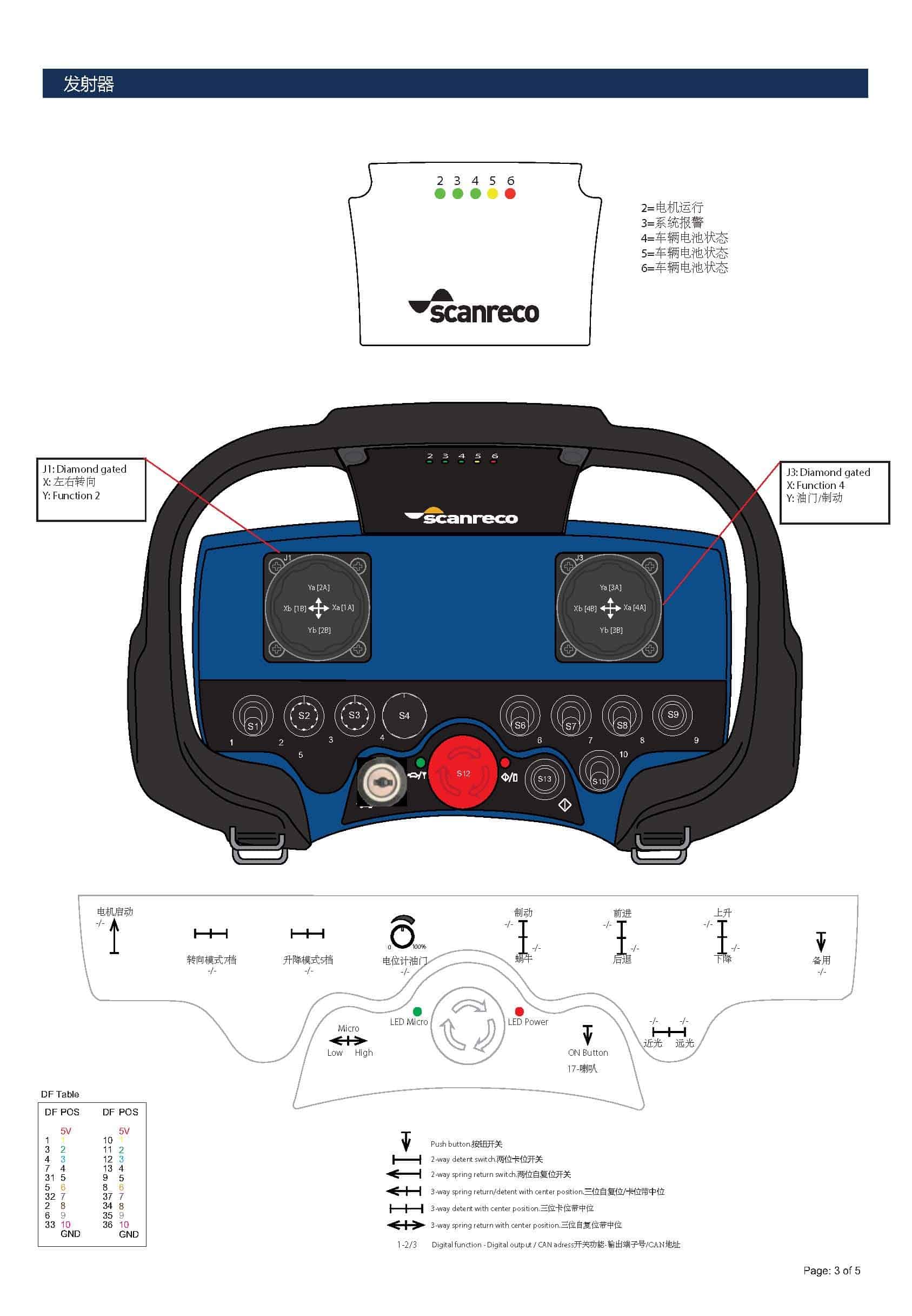
The remote control system connected through the data cable is the most basic accessory for controlling electric SPMT equipment. It includes a shock-resistant synthetic material, a control panel, a selector switch, and a joystick. Its comprehensive protective shell protects the joystick when the controller accidentally falls to the ground. For the operators who use it, its unique strap and arc design are more in line with the ergonomic design concept, allowing users to get maximum comfort using experience.
The remote controller is waterproof, windproof and shockproof, and it is also with UV-proof parts. Meet with the requirements of the EU Machinery Directive 2006/42/EC.
The remote controller can switch to wirelessly or wired modes.
Detailed Specification Sheet, Spare Parts List, and Tools List
Please contact us if you need a detailed specification sheet, spare parts list, and tools list.